Built in the 1950s, the plant had outdated and insufficient as-built data, making it difficult for engineers to design the expansion with adequate tie-ins from the new to the existing facility.
The Hess Tioga natural gas processing plant (TGP) in northwestern North Dakota recently underwent an expansion to equip the facility to meet demand for processing the increased natural gas production coming from western North Dakota’s oil fields. Previously, the plant was able to process approximately 120 million cubic feet of natural gas daily. The plant expansion more than doubled Hess’ processing capacity to 250 million cubic feet a day. Built in the 1950s, the plant had outdated and insufficient as-built data, making it difficult for engineers to design the expansion with adequate tie-ins from the new to the existing facility. To facilitate the expansion, Hess needed an as-built model of sections of the existing plant to support the design and engineering efforts. Already familiar with laser scanning and as-built data gathering from a previous expansion project for the Hess gas plant in Seminole, Texas, the project manager for the Hess Tioga project looked to Wood Group Mustang (Mustang) to provide as-built conditions in certain areas of the existing plant.
Company
Wood Group Mustang
(Mustang)
Location
Houston, TX
Solutions
Leica ScanStation 2
Leica Cyclone Software
Leica Cyclone Object
Exchange (COE)
Leica TruView software
Leica CloudWorx Software
Intergraph CADWorx Software
Simultaneous Design and Construction
The Hess Tioga plant expansion, located adjacent to the current Tioga plant, would facilitate ethane recovery, full fractionation and sales of natural gas liquids. The Hess TGP expansion included the design and construction of a new early flare system for the existing plant in order to relocate the existing flare to make room for the expansion. This new early flare system was installed and commissioned in August 2011. Meanwhile, the main plant expansion project to double processing capacity began in June of 2010, with design completion expected by August 2012.
The initial scope of work on the Hess expansion project was for Mustang to scan various portions of the existing plant that were associated with the early flare system upgrade and to provide data for the overall plant expansion FEED study. No tie-ins had been identified when the laser scan/survey team performed their initial fieldwork in August of 2009.
David Stevens, a piping designer and laser scan coordinator within the Mustang Laser Scanning/Special Projects Group, says, “The existing plant sits on 80 acres of land. We had large areas to laser scan and survey, particularly since we did not know the exact locations of the final tie-ins. Then the new plant expansion added another 15 acres to the plant.”
Mustang would need both time-of-flight and phased-based technology to complete the scans on the 80+ acres.
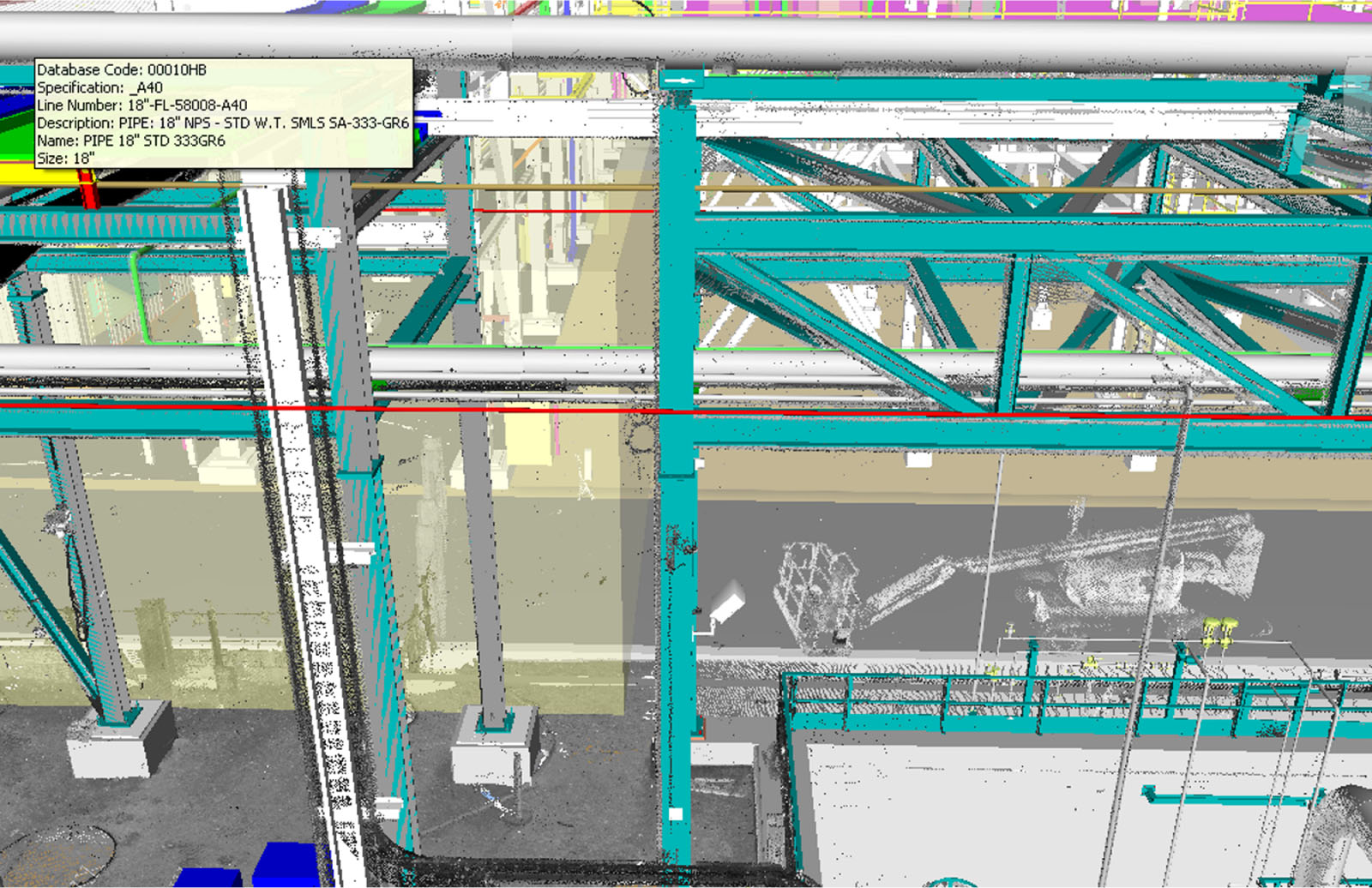
Mustang used CADWorx, Intergraph’s plant design and modeling solution, to create intelligent 3D models from the laser scan data. Within CADWorx Plant, designers were able to lay out existing vessels, tanks and various other plant equipment using real-world coordinates.
Increasing Scope
…The combination of time-of-flight and phased-based scanning gave us the ease of making big jumps throughout the plant with limited need for conventional surveying…
Mustang started utilizing laser scan technology on brownfield projects in 2005 with a HDS3000 time-of-flight scanner, the standard at the time for long range scanning required for topographic surveys or as-built data gathering. In 2006, the firm purchased the HDS6000 phased-base scanner to speed workflows. Phase-based scanners were able to gather over one million points per section compared to time-of-flight, which collected up to 50,000 points per second at that time. Then, with the introduction of the ScanStation 2, the company upgraded its HDS3000 to get the extra speed associated with the time-of-flight system. Both time-of-flight and phase-based scanners are highly accurate.
Stevens says, “The combination of time-of-flight and phased-based scanning gave us the ease of making big jumps throughout the plant with limited need for conventional surveying. In fact, our survey efforts primarily focused on locking the laser scan data to the existing plant grid and ensuring that the data was level for design.”
Laser control was set up utilizing a Leica TS1200 total station. The scanning team registered the laser scan data to two different sets of control – the local plant grid and the plant’s state plane coordinates. The laser scan team gathered the initial scope of work area using 355 scan positions, 313 using the HDS6000 and 42 using the ScanStation 2. The data was delivered to the original engineering firm contracted to perform the initial FEED study and the design of the early flare system.
Once the flare system had been designed and the associated tie-ins located, Mustang was awarded the detail design of the balance of the plant upgrades, including the development of the current as-built plant sections. This second effort required 278 laser scan positions. Mustang used the HDS6000 for 259 scan positions, and the ScanStation 2 documented another 19 scan positions.
Once the early flare system was installed, the laser scan team returned to the facility and did a complete as-built of the newly installed system with the HDS6000, adding another 131 scan positions. The scan team set 764 scan positions to gather all of the information needed for both design and engineering.
Stevens recalls, “With the right scheduling and the cooperation of the engineering, design and operations staff, we were able to perform the entire laser scan and survey work during the summer months of June through September.”
And Mustang’s laser scanning scope of work grew again. Stevens adds, “During one of our trips to the facility, the client asked us to laser scan an 80 acre section located across the highway from the gas plant, of which 35 acres is already utilized (by the electrical utility companies in the area).”
This area was to be used for construction office trailers and parking, as a staging area for equipment, piping and construction supplies, and as a source of fill dirt for the expansion site. The scan data was used to create topography maps as well as to locate power line clearances and other obstruction locations across the property.
And Mustang’s laser scanning scope of work grew again.
Post-Processing and Registration
Once back at the office, the survey team post-processed and registered the scan data within Leica Cyclone software and created TruViews, which are placed in both the engineering and multiple discipline design folders for easy access to the whole team.
“We utilize Leica Cyclone on 95% of our projects to post-process point cloud data,” says Stevens.
Using the Cyclone Object Exchange (COE), the point cloud model was exported to AutoCAD where designers launched CADWorx, Intergraph’s plant design and modeling solution, to create 3D intelligent models. Within CADWorx Plant, designers were able to layout existing vessels, tanks, and various other plant equipment using “real world” coordinates.
Stevens adds, “The equipment was quickly and easily modeled in 3D using Leica CloudWorx for AutoCAD tools to represent the equipment shape for visual reference, helping establish the overall plant site model, which would make it easier to review the new proposed project for those not familiar with the site.”
More detail could be applied in the event an existing vessel was to be tied into or used to fabricate an addition. For instance, the design engineer can determine a nozzle orientation using the point cloud and CloudWorx tools and then model the nozzle in CADWorx. With that level of detail, designer knows that the tie-in location to the vessel is accurate and will be called out on the subsequent isometric drawing. Along with equipment, existing buildings were modeled from the point cloud to help the designer find and mark the penetration coordinates for call out on the isometric drawing.
Coordination and Corrections
Originally, the post-processed laser scan data was handed over to the engineering firm selected to perform the front-end engineering and design (FEED) study of the overall plant expansion as well as the flare expansion. Once the FEED study was completed, Mustang was awarded the detail design of the project, which includes the development of isometric drawings from the 3D intelligent models.
The model for the FEED study was also created using CADWorx. The FEED study model was subsequently provided to Mustang to determine tie-in locations for the newly constructed flare relocation facilities. After relocation of the flare, the Mustang Laser Scanning/Special Projects Group went back to the plant to scan the new area and added this scan to the original point cloud model.
Tie-in locations to the new flare systems were then modeled to real world coordinates of the point cloud for seamless field fabrication fit up for tie-ins.
“The point cloud comparison was done by back modeling the point cloud tie-in locations using CloudWorx to determine the coordinate and then modeling a flange and stub in pipe with CADWorx Plant,” says Stevens. “These components were then marked as ‘existing’ and placed on their own AutoCAD layer. Once the isometric was created, these components would display on the isometric as the original tie-in points.”
With that level of detail, the designer knows that the tie-in location to the vessel is accurate and will be called out on the subsequent isometric drawing.
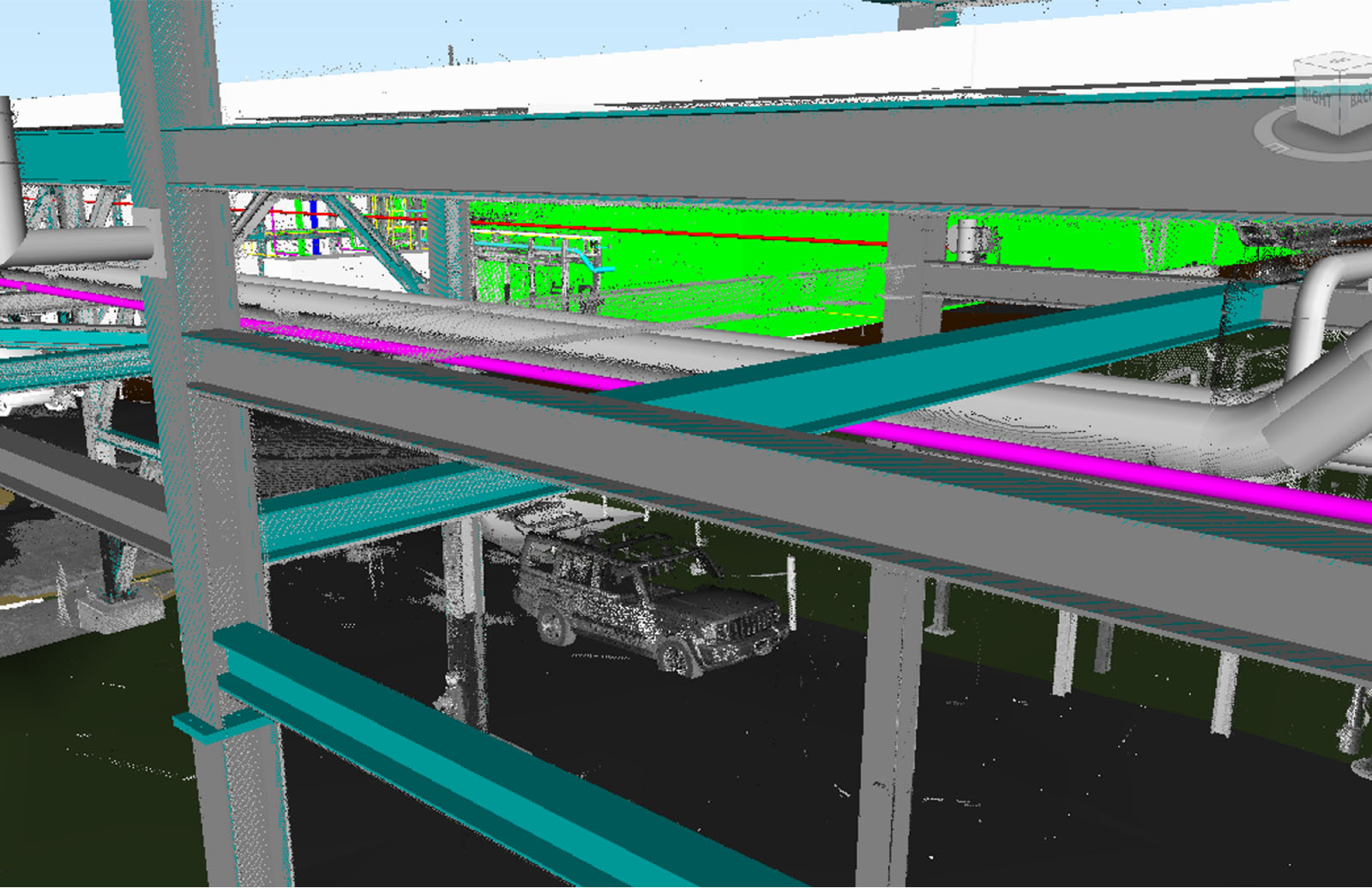
Point clouds were used during model reviews to resolve potential problems before they occurred. Having immediate access to exact as-built conditions kept the project on track.
Model-to-Field Improvements
Conventional walk down practices without laser scanning often require multiple trips to the field to verify locations and various obstacles happened frequently and required numerous personnel in the plant.
“With laser scanning, we were able to minimize occurrences in the field to just a handful, particularly important due to weather constraints in North Dakota,” says Stevens. “With safety an utmost importance, the number of individuals entering the plant is also drastically reduced.”
The project team used the point clouds during model reviews to resolve potential problems while in the office. Many questions are easily answered after overlaying a portion of the scan over the CADWorx model. For more detail, the TruView files provided photo quality visualization to the user. As well, designers had an immediate reference to exact as-built conditions, so there was no slow down waiting for more detail from the field.
Stevens concludes, “Through scanning data, we were able to provide an enormous amount of data that would not have been available through a conventional survey effort. That same data provided benefit through construction with the creation of isometrics and the resolution of field issues and will provide a solid foundation for lifecycle maintenance of the facility.”
Construction of the Hess Tioga Gas Plant expansion was completed in May 2014.
Networking with Natural Gas
For the Hess Tioga Gas Plant expansion, Mustang was also asked to create a network for easy access to the point cloud data and train the FEED contractor design staff in the use of the data.
Mustang used its EnterpriseElite (EE), a tool that simplifies software license management, to maintain a laser scan data server where 100% of the scan data is stored and accessible to multiple approved designers and design disciplines at the same time. Leica Enterprise Elite includes a new Subscription Licensing Program (SLP) that simplifies enterprise-wide deployment of all the Leica Geosystems High-Definition Surveying™ (HDS) software products and the associated data.
“Before the advent of EE, we would have to either provide an external drive to every designer and engineer on a project that need to utilize the data or we would have to copy the laser scan database onto each person’s desktop,” says Stevens. “It was time-consuming and costly. For any given project, our software costs alone were over the top. With the new system, the design teams are able to place the 3D point cloud data into their current project models.”
Each month, Mustang monitors its cost with the built in reporting tool and compares usage with the project timesheet to ensure that the software is billed accordingly. The company has ongoing projects that are utilizing CloudWorx for PDMS, AutoCAD and PDS (MicroStation).
“The EE software allows us to have a ‘fixed’ annual cost for maintenance and then we are able to ‘charge back’ each of the projects based off usage of the various CloudWorx software suites,” says Stevens. “With that one EE license, we are able to keep all of our projects going at the same time without worrying about who is working with what. The EE has enabled us to free up time for our Software Administrative people so they can work on other things in regards to helping to make projects successful.”
HIGH-VALUE DELIVERABLES
- High resolution registered point clouds
- Proprietary EnterpriseElite (EE) laser scan data server
BENEFITS
Increased Safety
All data captured from ground level with fewer personnel
Comprehensive Data Capture
Complete and accurate as-is dataset can be reused for future projects
Reduced Downtime
Perfect-fit installation means no rework
Better Project Visualization
3D models enable stakeholders to make better decisions