Documenting the actual placement of new construction is a way to accelerate project turnaround, reduce rework during equipment installation, and of course provide a 3D record for ongoing maintenance and operations.
As companies around the world strive to understand the age of digital transformation and how it changes workflows, geomatics professionals are using 3D laser scanning to accelerate the transition at a rapid pace. This is no surprise; the ability of laser scanning technology to accurately collect huge amounts of location data made it, right out of the gate, perhaps the most important tool for engineers and designers seeking the digital data they need to efficiently expand and renovate manufacturing facilities. Knowing the precise placement of existing ductwork, conduits, machinery, and equipment in a plant or factory makes it possible to perform clash detection before new equipment is installed and can reduce up to 95% of the amount of rework and change orders that usually plague such work.
Location
Vance, Alabama
Today, 3D digital data from laser scanners is also being applied to as-built and construction verification surveys. By performing such surveys quickly—during construction or immediately after—contractors can confidently verify that facilities are being built to match design. This, in turn, makes installation and operation of prefabricated modules and plant equipment far more efficient as well as facilitating smart building apps and the Internet of Things (IoT).
Phoenix-based Darling Geomatics has been doing this kind of work since 2002. In early 2018, the firm accomplished a potentially groundbreaking milestone that combines the two disciplines. “We were asked to verify that the 1.5 million square feet of expansion at the Mercedes-Benz U.S. International (MBUSI) automotive plant in Vance, Alabama, met construction specifications,” explains CEO Mary Darling. “This was shortly after building construction was completed, but before most of the manufacturing equipment had been moved in. Documenting the actual placement of new construction was a way to accelerate project turnaround, reduce rework during equipment installation, and of course provide a 3D record for ongoing maintenance and operations.”
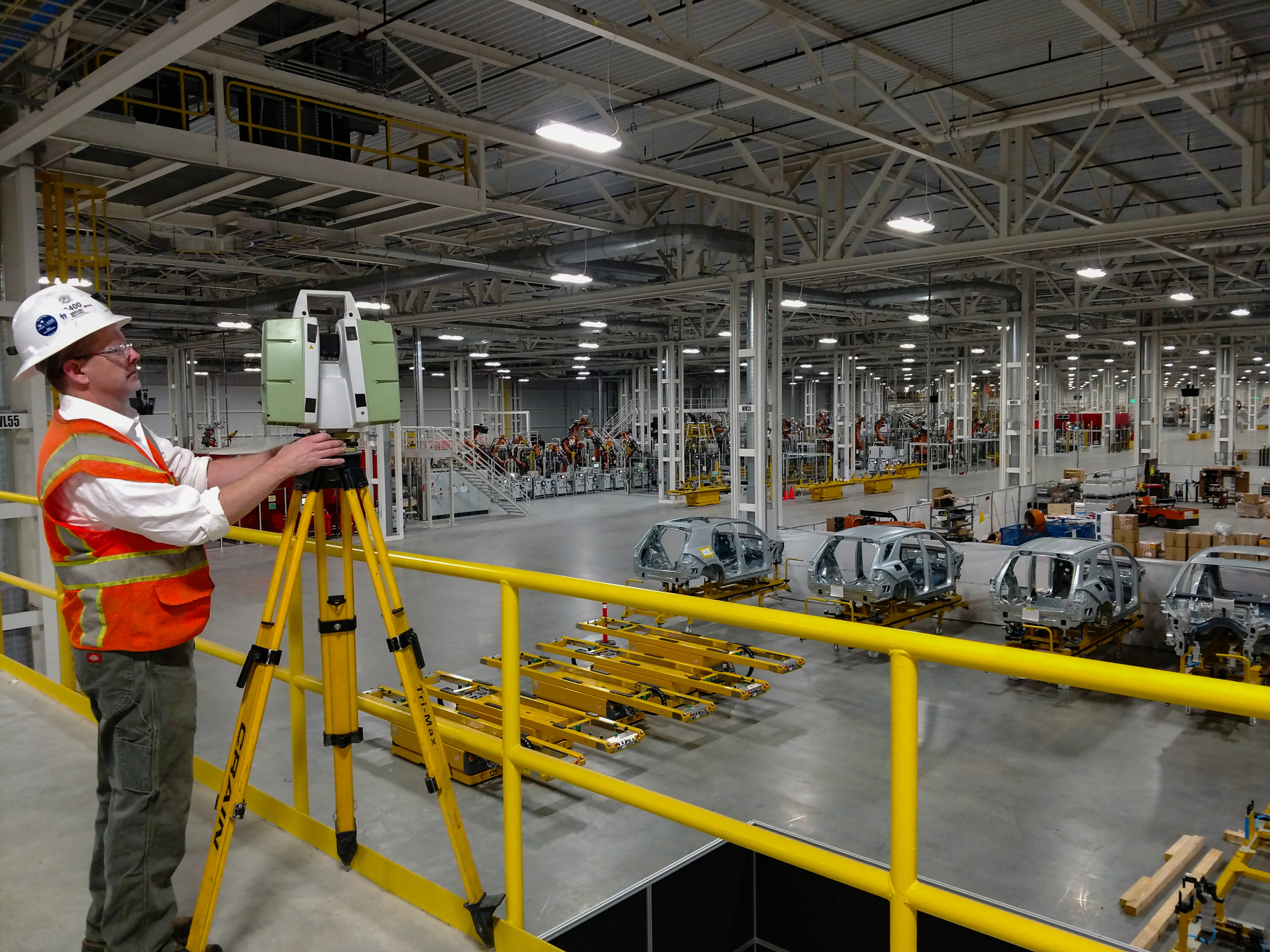
Billions of Digital Data Points in Just Eight Days
Using all Leica Geosystems scanners is a good way to keep our data consistent, especially since we use Leica Cyclone software for processing
The project was ideal for 3D laser scanning, but it also presented some challenges. “In this case, we were working for the general contractor,” says Darling 3D Scanning Division Manager Charlie Warren. “Mercedes-Benz is pretty particular with their specifications, and they felt a scan was the best way to verify that all their work was according to design. That part is standard for us, and we let them know that we work to a tolerance of six millimeters. What made this project different was the sheer size—1.5 million square feet is a lot of space, especially with all the ductwork and conduits being installed. And some equipment, including robots, had already been moved in. So mainly this was a big project, with some complications, and a relatively short window to get the work done on site.”
To prepare, Warren looked over the drawings and devised a plan that took advantage of the layout. “The expanded facilities were on a grid and featured a large number of manufacturing bays,” he says. “So it was relatively easy to plan our scan setups and sequences to avoid excessive overlap.” He also arranged for three scanners to be at the Mercedes-Benz plant for the entire eight-day time window. All were made by Leica Geosystems, an important part of Darling’s proposal: “These scanners bring excellent data quality and accuracies < ¼ ″ (6mm), while also being highly portable and quick to set up.”
Data consistency was also important. “Using all Leica Geosystems scanners is a good way to keep our data consistent, especially since we use Leica Cyclone software for processing,” Warren explains. “For this project, we used our own C10 and P20 scanners and brought in another specialist with a P30. All of them had the range and accuracy we needed here, and they all worked together well.”
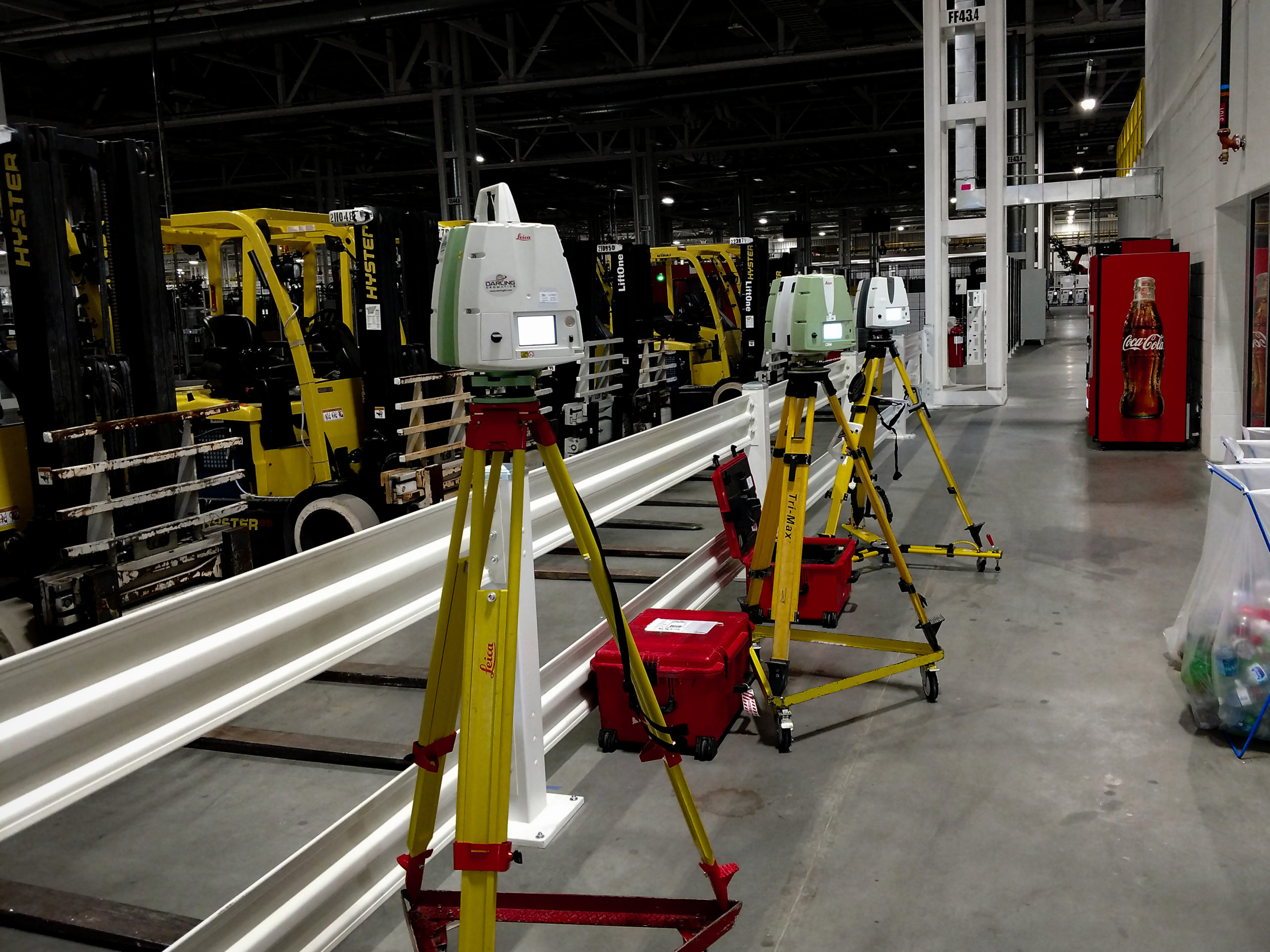
The scanners did have different specialties, though. “For tighter spaces we used the P20—it’s just so fast. And the C10 was a better choice for the longer shots we used to get onto the local survey coordinate system. But really, all three scanners were up to the task, and we gathered billions of accurate points that all registered precisely.”
One trick that helped the three-man/one-woman crew move quickly was wheeled tripods, which worked extremely well on the plant’s smooth concrete floors. “We have tripods for all our scanners,” explains President Richard Darling. “We fabricate them ourselves and developed this methodology when we scanned the San Francisco airport. Especially on a project this size, it saves time on setups and just moving the scanners around.”
Saving time was important; in just eight days, the team scanned billions of points from 920 setups, including shots to interior and exterior control points to keep the scan data on the same basis as construction. All the data collected was good, and it all registered easily into the software needed for comparison to the Navisworks design model provided by the general contractor.
Without 3D scanning and construction verification software tools, spot checks at various locations throughout the manufacturing plant would have taken considerably more time, provided only a fraction of the detail and introduced the risk of human error. Tape measures, single beam laser measurement tools and other data gathering methodologies pale in comparison to 3D scanners when it comes to the quantity and accuracy of measurement data collected over a given time period.
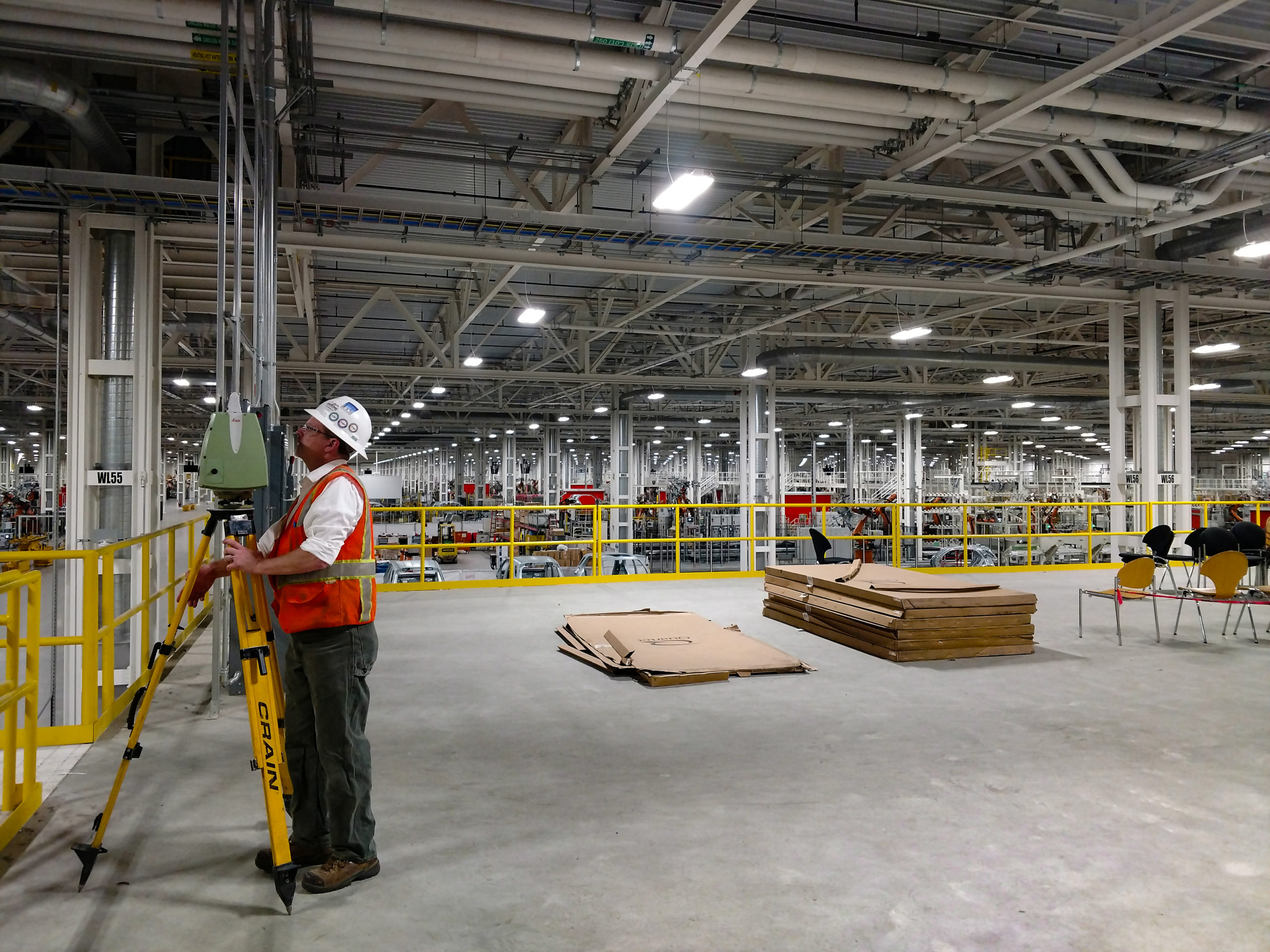
Excellent Construction, Verified
Darling’s work was able to prove that all major construction components—steel, concrete, ducting, etc.—were exactly in place (within a 1/2 inch), and that even less consequential elements, like lighting, were within 2 inches of design.
The news was good. Darling’s work was able to prove that all major construction components—steel, concrete, ducting, etc.—were exactly in place (within a 1/2 inch), and that even less consequential elements, like lighting, were within 2 inches of design. It seems like a lot of work just to confirm that new construction is where it’s supposed to be. But really, it wasn’t a lot of work—just four people and three scanners for eight days, and several weeks of office time. That’s a minor line item on a project of this size, and even that cost was more than covered by the greater confidence and efficiency made possible when designing and installing the actual automobile manufacturing equipment. Put simply, using digital data composed of billions of accurately scanned points to perform high level quality control was an investment that paid off for all stakeholders.
DOWNLOAD THE PDF